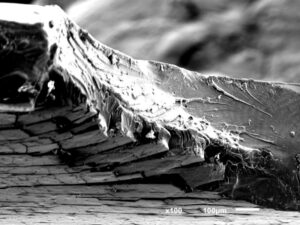
Labor für Schadensanalysen nach VDI 3822 an metallischen, polymeren und keramischen Bauteilen nach Rissen, Brüchen oder Korrosion: Trotz sorgfältiger Planung, Konstruktion, Produktion und erfolgreicher Testläufe kann es auch im Normalbetrieb zu Fehlern und Schäden an technischen Komponenten kommen. Wir helfen Ihnen den Primärschaden ausfindig zu machen, dessen Schadensursache zu klären und Abhilfemaßnahme festzulegen. Somit können Sie Schäden und finanzielle Verluste in Zukunft verhindern! Unsere Abhilfemaßnahmen beziehen sich dabei auf alle Bereiche: Konstruktion, Fertigung, Werkstofftechnik und Betriebsbedingungen.
Schaden | Ursache | Untersuchungsmethode |
Risse und Brüche | Überlastung, Materialermüdung, unzureichende Werkstoffwahl, thermische Spannungen | Makroskopie, Mikroskopie, Metallographie, Röntgen- oder CT-Untersuchung, SEM |
Korrosionsschäden | Umwelteinflüsse (Feuchtigkeit, Salz), falsche Materialwahl, mangelnder Korrosionsschutz | Korrosionsprüfung, REM-EDX, chemische Analyse, Metallographie |
Abrieb und Verschleiß | Mechanische Belastung, falsche Schmierung, unzureichende Materialwahl | Abriebtest, Verschleißanalyse, Oberflächenanalyse, Mikroskopie, REM, Metallographie |
Lunker und Porosität | Einschluss von Gasen während der Fertigung, falsche Schweißparameter, unzureichende Kühlung | Röntgenprüfung, Ultraschallprüfung, Metallographie, CT |
Überhitzung und Aufhärtung | Zu hohe Schweißgeschwindigkeit, falsche Wärmebehandlung, unzureichende Kühlung | Härteprüfung, Mikroskopie, metallographische Analyse |
Spannungsrisse | Hohe innere Spannungen, unzureichende Entspannung nach dem Schweißen, falsche Fertigungstechnik | Röntgen- oder CT-Untersuchung, Spannungsanalyse, Metallographie |
Verzug und Deformation | Falsche Bearbeitungsprozesse, unzureichende Stabilität während der Fertigung | Deformationsmessung |
Schweißnahtfehler | Fehlerhafte Schweißtechnik, unzureichende Vorbehandlung, falsche Schweißparameter | Metallographie, Schweißnahtinspektion, mikroskopische Analyse, Chemische Analysen |
Verschmutzungen und Ablagerungen | Kontamination durch falsche Werkstoffe, unzureichende Reinigungsprozesse, Umwelteinflüsse | Mikroskopische Analyse, chemische Tests, REM-EDX |
Materialermüdung | Wiederholte Belastung, unzureichende Werkstoffauswahl, falsche konstruktive Gestaltung | Rissinspektion, Metallographie, SEM |
Freilegen eines Risses
Triboligieverschleiss an einer Nockenwelle
Korrosion an einer Schweißnaht
korrodierte Schweißnaht einer Gaslanze
Defekte Schweissverbindung einer Leitung
Ausbruch an Zahnflanke eines Getriebes, Windkraft.
Brandschaden defekte Elektronik
Riss durch SMD Bauteil
gebrochenes Kabel Durchstrahlungsaufnahme
geplatzter Schlauch
Gesellschaft für Werkstoffprüfung mbH
Qualität sichern | Entwicklung begleiten | Schäden analysieren | Wissen weitergeben